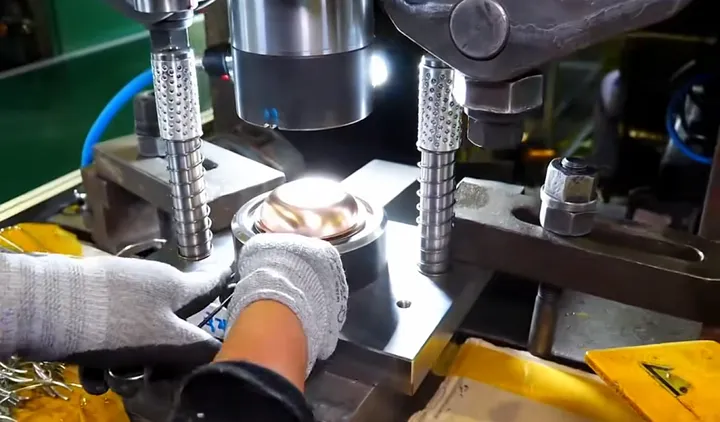
Combining extrusion & metal stamping to customize your metal parts
There are four methods used in the metal forming industry to create products, parts and component. These four primary methods are extrusion, stamping, roll forming, and press brake bending. Under most conditions, each of the different methods are completed independently with stamping being the most commonly used. The choice of which metal forming method to use is based on various factors with cost being one of the most prominent.
In most cases, aluminum extrusions are valuable on their own without the need for any other procedures or secondary processing. As with all forms of aluminum products, aluminum extrusions are lightweight, strong, have a high strength to weight ratio, and are corrosion resistant. These factors are the main reason that aluminum is so widely used in a variety of applications.
Regardless of the exceptional properties of aluminum extruded products, there are cases where aluminum extrusions require the use of finishing processes to transform them into final quality products. Included in the set of processes are forming, machining, and surface finishing, each of which are completed to change the appearance, texture, and shape of an extrusion to make it comply with the requirements of design parameters.
Aluminum Extrusion
Extrusion involves taking an aluminum billet and pressing it against a die using mechanical or hydraulic tools. It is a continuous or semi-continuous process that is used to form a wide range of aluminum products in accordance with a designed profile. The results of extrusion are highly durable and long-lasting products that are used in construction, manufacturing, and various other applications.
As the aluminum passes through the die, it takes on the shape of the profile. The range of products that are produced by extrusion include rods, bars, seamless round tubes, square tubes, rectangular tubes, triangular shapes, hexagonal shapes, and channels. Aluminum extrusion is capable of producing any form, shape or configuration regardless of how complex it may be. Extrusion engineers and designers take provided parameters and use them to create dies with the profile of the desired shape.
Although some of the shapes produced by extrusion may be the final product, such as tubes and channels, in some cases, extrusion produces components for a larger assembly, which includes a countless number of products. For doors and windows, extrusion is used to produce rigid framing materials, weather stripping, and frame reinforcements. The trim, edging, and tubing for appliances are made using extrusion. The endless list of types, kinds, and patterns that are produced by extrusion includes unique and specialized components that are designed to fulfill specific requirements.
Stamping
Stamping is a cold metal process that uses dies to shape, form, and produce complex parts and components. The stamping process includes blanking, bending, punching, and piercing, which are engineered to produce various types of shapes or configurations. Stamping, also known as pressing, involves flat sheets of metal that are placed in a stamping press where the die with the desired shape is pressed against the metal sheet under a great deal of pressure.
In aluminum extrusion, stamping is a method for finishing and shaping an extruded component or part into a desired shape that cannot be achieved by extrusion alone. Although stamping is a machining process onto itself, in the case of extrusion, it is a secondary finishing process that is used to further shape and form an extruded workpiece.
Stamping Used on Extruded Parts
The flexibility of extrusion makes it possible to create a wide myriad of shapes and configuration. What is not possible with extrusion is the inclusion of other features such as bending, openings or holes, embossing, flanging, and coining since the extrusion process pushes aluminum through a die to form a long and continuous form that can be cut to a specific length.
Placement of Holes or Openings
The creation of openings in extruded materials can be completed several ways with each method being labor-intensive and time-consuming, which interferes with lead times and on time deliveries. Unlike the manual methods for placing holes in extrusion, stamping completes the process quickly and efficiently in a fraction of the time that is required for drilling or punching. In modern industrial operations, computer numerical control (CNC) machines are used due to their precision and accuracy.
Once a workpiece has been formed by extrusion, it is placed in a CNC machine or stamping press where holes are placed in the workpiece in one cycle or stroke of the press, a process that takes seconds or a few minutes. With the one stroke of a stamping press, a workpiece is shaped and formed to design parameters.
The diameters and sizes of openings that can be placed in a workpiece vary with the type of stamping die and the shape of the extruded workpiece. Using stamping to add openings to a workpiece ensures that the openings are within required tolerances and meet design requirements and dimensions, which is unlike manual placement of holes that can be inaccurate and outside tolerances. After holes are added to an extruded workpiece, they may need to be tapped or threaded.
Bending
A very common stamping process that is completed on extruded aluminum is bending since designs for appliances, windows, and doors require that channels and weather stripping follow the contours of a product. The bending process involves deforming aluminum along a straight axis and is used to achieve any type of bend angle with 90o bends being the most used and most common.
The bending process is very carefully completed to avoid spring back and overbending. In the case of spring back, it is the tendency of material to attempt to return to its original straight shape after force is applied, which necessitates precision professional control of the bending process. Overbending is bending an aluminum workpiece beyond its limits and is another reason for constant monitoring.
Flanging
Another very common stamping process that is used on extruded aluminum is flanging where an opening in an extrusion is bent at 90o along a curved axis to form a ridge, lip, or rim that can be internally or externally located depending on design parameters. Flanges are included in designs for easy attachment of components or for stabilizing and guiding. The use of flanges on extruded aluminum gives parts greater flexibility and ensures tight secure joining of components.
The three stamping processes that are listed above are a few of the methods used to deform aluminum extrusions to match design requirements. They are added features that enhance the capabilities of an aluminum extrusion and make it compliant with the requirements of an application.
Conclusion
The process of aluminum extrusion has been used for centuries to create unique shapes and forms that are required for industrial applications. Although the designs created by extrusion are of the highest quality and meet performance standards, there are aspects of their use that require the addition of other features. In this particular case, stamping is used due to its ready availability and efficiency. By applying a sufficient amount of force, an aluminum extrusion can be bent, shaped, and deformed to meet the requirements of a design.