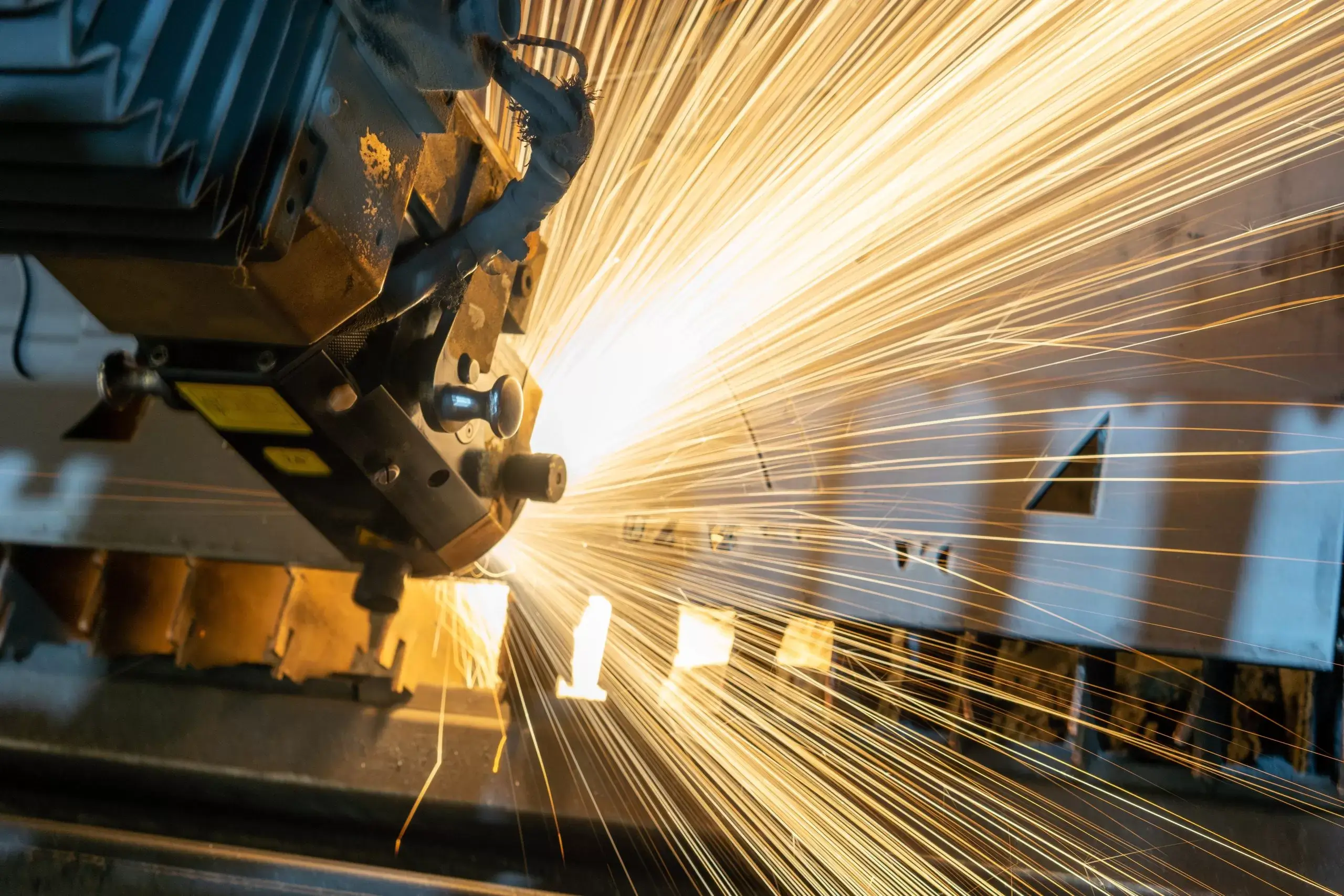
Metal stamping is a manufacturing process that involves shaping flat metal sheets into specific forms through dies and punches. This process is widely used in the automotive, aerospace, electronics, and appliance industries.
Properly selecting materials is crucial in metal stamping, as it directly affects the final product's quality, cost, and durability. Choosing the wrong material can result in product failure, production delays, and increased costs.
This article will discuss the types of materials commonly used in metal stamping, the factors to consider when choosing materials, how to choose the proper materials, and the common problems encountered with improper material selection. By the end of this article, you will better understand how to choose the right materials for your metal stamping project.
Types of Materials Used for Metal Stamping
Two main categories of materials are used in metal stamping: ferrous and non-ferrous. Ferrous materials contain iron, while non-ferrous materials do not. Below are some common materials used in metal stampings, including some specific applications, and beneficial qualities for each that could influence one’s choice.
Ferrous Materials
Carbon Steel
- This material is made of iron and carbon and is known for its strength and durability. It is also relatively inexpensive and can be easily formed into different shapes. Carbon steel is available in various grades, each with different carbon content levels and other alloying elements. Low-carbon steel is softer and more formable, while high-carbon steel is stronger and more difficult to form. Carbon steel can also be coated with zinc, nickel, or chrome for added corrosion resistance. Carbon steel is commonly used in the automotive industry, the construction industry household appliances, industrial equipment, and the agricultural industry.
Stainless Steel
- This material is a type of steel that contains chromium, which gives it its corrosion resistance. It is available in various grades, each with different corrosion resistance, strength, and machinability levels. Stainless steel is commonly used in applications where the final product is exposed to harsh environments, such as marine, food processing, or medical equipment.
Galvanized Steel
- This material is made of carbon steel coated with a zinc layer, which provides added protection against corrosion. The galvanizing process involves dipping the steel in a bath of molten zinc, which creates a bond between the zinc and the steel. Galvanized steel is commonly used in outdoor fencing, roofing, and gutters.
Non-Ferrous Materials
Copper
- This material is highly conductive and has excellent corrosion resistance. It is commonly used in electrical and plumbing applications, as well as in decorative applications, due to its attractive reddish-gold color. Copper is also a soft metal, which makes it easy to stamp and form into different shapes.
Brass
- This material combines copper and zinc and is known for its bright gold-like appearance. It is commonly used in decorative applications such as hardware, ornaments, and musical instruments. Brass is also a relatively soft metal, which makes it easy to stamp and form.
Aluminum
- This material is lightweight, strong, and has excellent corrosion resistance. As a result, it is commonly used in the aerospace and automotive industries and in consumer products such as appliances and electronics. Aluminum is available in various grades, each with different strength, corrosion resistance, and formability levels. It can also be coated for added protection against corrosion.
Factors to Consider When Choosing Materials for Metal Stamping
When selecting a material for metal stamping, it is important to consider the specific properties required for the final product. For example, durability, formability, thickness, hardness, and corrosion resistance should be considered. These qualities are explained in greater detail below.
- Durability
- Durability refers to the material's ability to withstand wear and tear, fatigue, and other forms of stress. The level of durability required will depend on the intended application of the final product. For example, a product exposed to heavy use or harsh environments will require a more durable material.
- Formability
- Formability refers to the material's ability to be formed into different shapes without cracking or breaking. The level of formability required will depend on the complexity of the part to be stamped and the type of stamping process to be used.
- Thickness
- The thickness of the material will affect its strength, formability, and cost. Thicker materials are stronger but less formable, while thinner materials are more formable but less durable.
- Hardness
- Hardness refers to the material's resistance to deformation, scratching, or abrasion. The hardness required will depend on the intended application of the final product. For example, a product subject to high levels of wear and tear will require a harder material.
- Corrosion Resistance
- Corrosion resistance refers to the material's ability to resist degradation due to exposure to moisture, chemicals, or other corrosive substances. The level of corrosion resistance required will depend on the final product's intended application and the environment it will be exposed to.
When selecting a material for metal stamping, it is important to consider all of these factors and determine the optimal combination for the specific application. For example, a product used in a corrosive environment may require a material with high corrosion resistance but may sacrifice some formability or durability. On the other hand, a product that requires intricate stamping may require a more formable material but may sacrifice some durability or hardness.
Common Problems Encountered with Improper Material Selection
Improper material selection can lead to various problems impacting stamped parts' quality, performance, and production. Here are some common problems that can arise from using the wrong material for metal stamping:
- Wear and Tear
- If the material is not strong enough to withstand the intended use, it may experience excessive wear and tear, leading to premature failure of the part.
- Tooling Damage
- The stamping process can cause significant stress on the tooling, and if the material is too hard or too soft, it can cause damage to the tooling, leading to increased tooling costs and production delays.
- Surface Finish Issues
- Some materials may be difficult to stamp or may result in a poor surface finish, which can affect the part's appearance, functionality, and overall quality.
- Production Delays
- If the material is unsuitable for the stamping process, it can lead to production delays and increased costs due to rework, tooling adjustments, or even the scrapping of defective parts.
These problems can have significant consequences, including increased costs, decreased quality, and reduced customer satisfaction. Therefore, selecting the appropriate material for metal stamping is crucial to avoid these issues and ensure that the stamped parts meet the required specifications and performance standards.
How to Choose the Proper Materials for Metal Stamping
Choosing the proper material for metal stamping requires carefully evaluating several key factors. Here are the main steps to follow:
- Determine the End-Use Application
- The first step is to determine the intended use of the final product. This will help identify the environmental conditions, load requirements, and other factors affecting the material's selection. For example, materials with high-temperature resistance may be required if the product is used in a high-temperature environment.
- Identify the Required Characteristics
- Once the end-use application is established, the next step is identifying the required material characteristics. This includes strength, formability, corrosion resistance, and hardness. These characteristics will depend on the specific requirements of the end-use application.
- Consider the Cost
- Cost is always a factor when choosing a material for metal stamping. For example, materials with high strength, formability, or corrosion resistance may be more expensive than those with lower performance characteristics. Therefore, balancing the cost with the required material characteristics is important to ensure the final product is effective and cost-effective.
- Evaluate the Fabrication Process
- The final step is to evaluate the fabrication process used to stamp the material. Different stamping processes require different material characteristics, so it is important to consider the specific process used. For example, if the stamping process involves deep drawing or other complex forming operations, materials with high formability may be required.
When evaluating different material options, it is also important to consider the material supplier's reputation and track record. Materials from reputable suppliers are more likely to meet the required specifications and have consistent quality. It is also important to work closely with the material supplier and the stamping service provider to ensure that the chosen material is appropriate for the intended application and the specific stamping process.
In summary, choosing the appropriate material for metal stamping requires carefully evaluating several key factors. By following these steps, selecting a material that meets the required specifications, is cost-effective, and can be successfully stamped into the desired shape is possible.
Conclusion
In conclusion, proper material selection is essential for high-quality, cost-effective metal stamping. By considering the necessary factors and working with a trusted material supplier, selecting the appropriate material that meets the specific requirements and delivers reliable, high-quality stamped parts is possible.
Factors such as durability, formability, thickness, hardness, and corrosion resistance should be considered when choosing materials for metal stamping. In addition, the end-user application and the specific fabrication process must also be evaluated.
Partnering with a trusted material supplier is also essential for successful metal stamping. A reputable supplier can help ensure that the material meets the required specifications, has consistent quality, and can be successfully stamped into the desired shape.
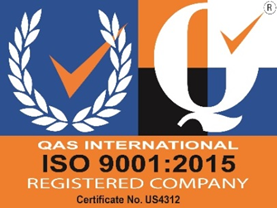