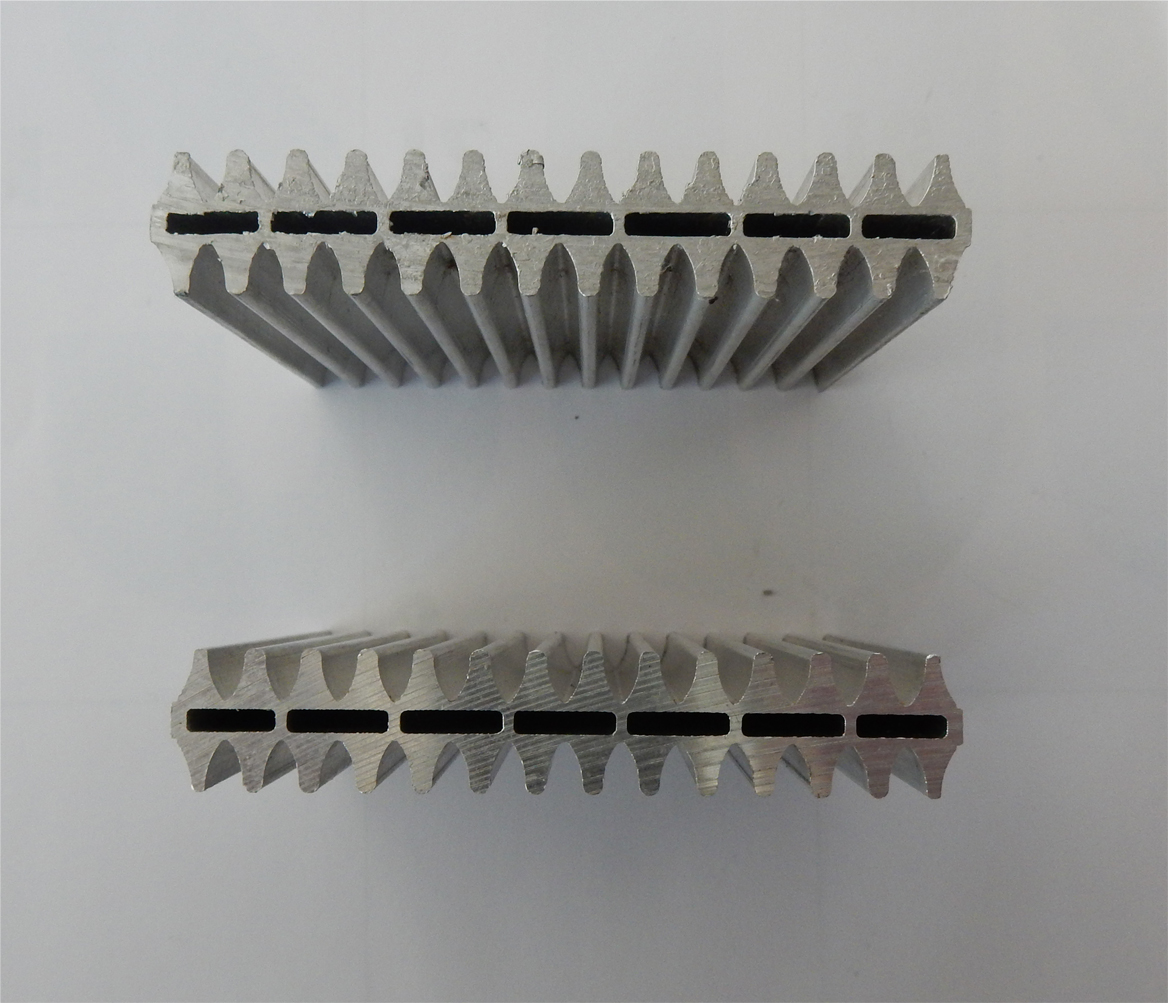
Aluminum extrusions are complex profiles that uniformly fit into the length, dimensions, and requirements of a design. Custom extrusions use the dimensions and configuration of a design to exactly match the needs of a special product or structure. The process of aluminum extrusions provides flexibility and adaptability that can enhance the strength and durability of a project.
The process of aluminum extrusion produces linear aluminum products with the strength to weight ratio of aluminum as well as aluminum’s cost-effectiveness. Using written details, CAD drawings, blueprints, or design dimensions, extrusion experts can make aluminum parts and products that perfectly match the size and shape of a design.
What is Aluminum Extrusion?
The mechanism of aluminum extrusion involves forcing aluminum alloy material through a tooling die that has the exact cross-sectional profile and dimensions of the final product. As the aluminum material passes through the die profile, it is squeezed such that it comes out in the desired shape. The process is used to produce common and simple shapes such as rods, bars, round tubes, square tubes, rectangular tubes, triangle shapes, hexagonal shapes, and channels.
The flexibility of the aluminum extrusion makes it possible to form any shape regardless of how complex. Engineers and designers can take the specifications for a design and transform it into a profile for the extrusion process. This includes complex shapes that may be the final product or ones that are used as a portion of an assembly. The nature of aluminum extrusion makes it possible to take any conceptualization and transform it into a reality.
The Aluminum Extrusion Process
The aluminum extrusion process begins with a rendering that is supplied by a client. Experts take the rendering, regardless of its form, and create a CAD drawing of a die that has the shape of the profile of the final product. Although the process of aluminum extrusion may seem simple, there are several complex engineering details that have to be precision calculated to ensure that the final outcome fits a customer's needs.
Steps to the extrusion process:
Step One – The Billet:
The extrusion process begins with aluminum that is in the form of a log or billet. The series of aluminum used for extrusion is alloy series 6000 formed in logs of 6 inches in diameter.
Step Two – Extrusion Die:
There are standard dies that all extrusion manufacturers use to create their common products. The round shaped dies are made of steel and are preheated before the extrusion process to reduce wear and ensure even metal flow.
Although there are several standard dies, in many cases, it is necessary to custom design a die to meet the specific needs of a project or part. This is completed with the help of extrusion engineering experts that take customer diagrams and drawings and turn them into a die.
Step Three – Heating the Billet:
The billet is preheated to 400o or 500o C to make it malleable for extrusion. It is sufficiently heated to be formable but not enough to make it molten.
Step Four – Extrusion Press:
The preheated billet has a lubricant or release agent applied to it before it is placed in the extrusion press. The lubricant prevents the billet from sticking to the ram that forces it through the die.
Step Five – The Ram:
The hydraulic ram applies several tons of pressure to the billet as it pushes it into the container of the extrusion press. As the pressure is applied by the ram the aluminum material expands and fills the walls of the container.
Step Six – Extruded Material:
The alloy material that has filled the container is pressed against the die as continual pressure is applied to it. The movement of the ram and the built-up pressure forces the aluminum material through the die opening where the fully formed profile emerges.
Step Seven – Run-out Table:
As the profile exits the die, it is gripped by a puller that guides it along the run-out table at a rate of speed that matches that of the extrusion press. On the run-out table, the profile is “quenched” or uniformly cooled by water or fans.
Step Eight – Shearing and Cooling:
When the extrusion reaches the length of the run-out table, it is sheared by a saw. Although the runout table cools the sheared extrusion, it is not sufficiently cool for processing and is transferred to a cooling room where it will stay until it reaches room temperature.
Step Nine – Stretching:
During the extrusion process, the profiles are naturally twisted, which needs to be corrected. In the stretching process, the profiles are gripped at each end and pulled until they are straight and brought to their specified shape.
In the steps of the extrusion process, the table length profiles are cut to their design lengths. Once they have been straightened and cut, the profiles are at T4 temper. In order to increase their temper to T5, they are placed in an aging oven.
As is indicated in the extrusion process, special and custom designs can easily be created to match unusual and unique design requirements. Engineering experts and design creators can take any form of rendering, drawing, graphic design, or approximation and develop an extrusion die.
Industries That Depend on Aluminum Extrusion
Aluminum extrusions have become a useful tool for many industries due to its strength to weight ratio and low cost. From standard tubes and rods to custom manufactured designs, aluminum extrusions offer many benefits that are not available in other metals. The properties of aluminum such as its strength, durability, light weight, and resistance to corrosion makes it an ideal structural material.
Industries that depend on aluminum extrusions include:
- Storage racks, cabinets, and workstations
- All-Terrain Vehicles
- Landscaping such as lawn mowers
- Construction including doors and window frames
- Recreation
- Gun manufacturing
- Electronics
- Lighting
All industries require custom designed and manufactured aluminum extrusions to enhance their products and improve product quality.
The QST Difference
QST produces high quality custom profile aluminum extrusions for pieces as large as 6” in diameter. We use the highest quality aluminum 6000 series up to T5 harness. QST is dedicated to meeting and exceeding the needs of our customers whether you want standard tubing and channels or require custom designed and manufactured designs for unique and special requirements. We are here to serve you and meet your needs.
Aluminum Extrusion Manufacturing in Wisconsin
Located in Jackson Wisconsin, our 40,000 sq/ft aluminum extrusion manufacturing facility operates a 300-foot extrusion line with auto feeders directly into our temper oven, giving us complete control from the first billet to the last.
Ready to get your project started?
Contact QST today for a free quote!